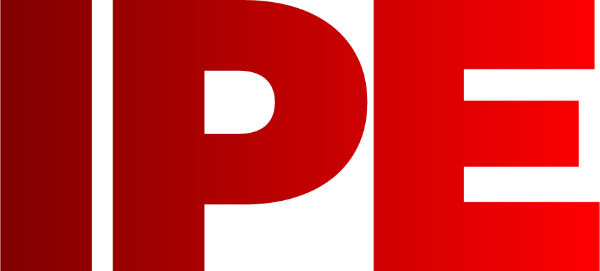
![]() |
Edward Lowton
Editor |
![]() ![]() |
Home> | Plant, Process & Control | >Boilers and burners | >Gas burners for drying facility |
Gas burners for drying facility
30 September 2018
Toll sprayer, Express Contract Drying (ECD), is gaining from process gas burner specialist, Lanemark Combustion Engineering's, technology on a series of drying facilities in South Wales.
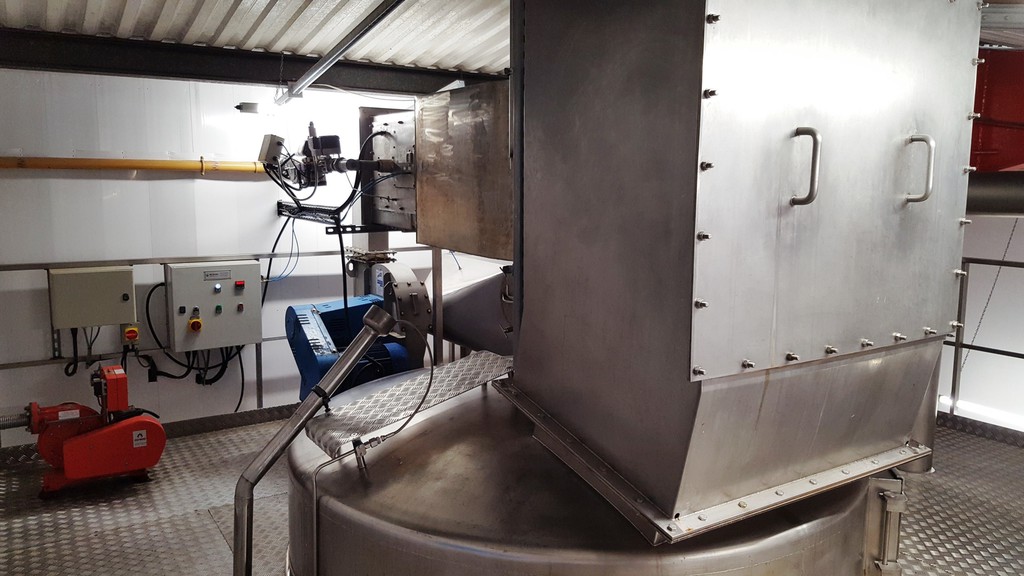
Nick Ball, operations director at ECD’s Ebbw Vale facility, one of two operated by the company in the area, explains the key role played by the Lanemark installations: “We have built a leading reputation over 35 years for the supply of dried food flavourings and colourings, mostly for the UK snack sector,” he says. “This is centred on five process lines which handle a combination of water, a carrier such as potato starch and the added flavour, all of which are blended into an emulsion that is then transferred to one of the processing vessels. Here, the action of the heat created by the Lanemark burner evaporates the water from the mixture to leave a powdered flavour that is then moved forward for packaging and despatch.”
Nick Ball points out that typically a moisture level of just 3% is achieved in this way. This is well within the industry standard of 5% and ideal for onward shelf life of up to a year.
“The installations at the ECD site feature our duct burner – or DB – design,” explains Adrian Cadman, process burners sales manager at Lanemark Combustion Engineering. “Each is fitted to a mounting plate that is bolted into the process air duct, acting as a transition box, with a fan then driving the heated air through connected ducting to the point where the emulsion is sprayed into the process.” Importantly, the designs, which also incorporate a panel, booster and exhaust fan, ensure there is no direct flame impingement on the product itself.Lanemark’s installations on all five vessels – with plans now well advanced for adding a sixth facility – all operate from the available natural gas supply and include the process air fan, a modulating gas valve train, control box and elements of the stainless steel ducting.
“It is also vital that we are able to closely control the heated air temperature to reflect variations such as volume, type of emulsion involved and even the size of the nozzle through which it is sprayed,” adds Nick Ball. “Each installation can deliver a required temperature level of, typically, between 180°C and 200°C, with excellent heat up and temperature stability characteristics.” The company also benefits from Lanemark’s BurnerCare service support package which includes a planned servicing programme that helps to ensure continuous plant operation.
The range of flavourings and coatings that can be produced at ECD’s Ebbw Vale facility not only reflects the versatility of the company’s operation but also the need for ongoing, reliable output. The role played by each of the systems supplied by Lanemark Combustion Engineering matches this need and is an excellent demonstration of the suitability of the company’s process gas burner technology to deliver precise process heating objectives in specialist sectors of the food processing industry.