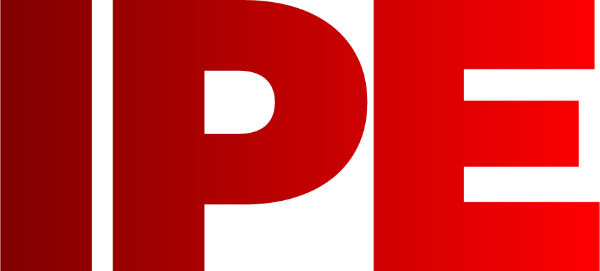
![]() |
Edward Lowton
Editor |
![]() ![]() |
Home> | Plant, Process & Control | >Compressors and ancillary equipment | >Optimising energy efficiency |
Optimising energy efficiency
11 July 2019
The British Compressed Air Society (BCAS) explores some of the areas to consider when it come to energy efficiency.
Compressed air is often referred to as the fourth utility, with the electrical energy used to drive air compressors equating to approximately 10 per cent of all the electricity used in the UK.
Widely accepted as a highly effective and safe form of energy for the manufacturing and process industries, generating the high-volumes of air demanded by the application can be energy-intensive.
A key challenge for operators therefore is to improve bottom line productivity by considering the total cost of equipment ownership over its entire life, rather than just its initial capital price.
This is important because over 80 per cent of this cost base can be in the system’s energy consumption and maintenance in the ten years after the initial purchase.
The move to greater efficiency
Even if a site purchases the most efficient compressor on the market but then connects it a system that has a 40 per cent leak rate, all they are achieving is to produce waste more efficiently! Compressed air users are now actively seeking the information they need to manage these issues.
Of course, the benefit of installing an efficient compressor package is only realised if it is installed as part of a system that is equally energy efficient. A compressed air system is just that, a system, and every element of it impacts upon its energy consumption. It is therefore a mistake to focus on only one aspect of the system to the exclusion of others, which will only result in missed opportunities to save energy.
To help operators make an informed choice, BCAS has produced a comprehensive whitepaper entitled ‘Reducing Energy Consumption from Compressed Air Usage’ which can be downloaded from the BCAS website at www.bcas.org.uk.
Maintenance and performance
Maintenance is also a vital part of the overall cost base, to keep both the efficiency and whole life costs of a compressed air system down. End users are realising that moving towards regular routine maintenance rather than reactive maintenance is far more cost effective and will help to reduce unplanned downtime.
In particular, with the continued emphasis on Industry 4.0 and intelligent data, many operators are benefiting from greater insight in to their compressor performance and are implementing predictive maintenance regimes, preventing potential system faults before they even occur.
Another area to consider is the increased uptake of data logging, with many suppliers now auditing the performance of an existing compressed air system in terms of energy consumption, peaks and troughs in demand and areas of inefficiency. In particular, with reference to the ISO 11011:2013 (Compressed Air – Energy Efficiency – Assessment) standard, users of compressed air are required to ask their energy auditors to work towards ensuring best practice.
The information obtained can then be used to recommend system improvements - from investing in new, energy-efficient equipment, to heat recovery options or simple upgrades to existing plant.
The current trend towards data exchange and increased automation in manufacturing is a positive move and is providing operators with far greater insight in to the performance, and efficiency, of their compressed air system. We are all aware that electricity accounts for a significant proportion of compressed air cost of ownership and therefore, finding new ways to minimise energy consumption is key.
Typically, this has been achieved by investing in new, energy-efficient machinery but now, with the availability of so much data, operators can realise far greater control over their existing compressor estate; monitoring performance parameters 24/7 if required to ensure the most efficient operation.
In addition, as a compressed air system represents a significant capital expense, operators should speak to their supplier about the finance options available. For example, some suppliers will offer the option to lease equipment or to pay for the air ‘as you go’, in the same way as company’s pay for their utilities, avoiding upfront capital expenditure while still enjoying the benefits of a new efficient system.
- WEEE2 directive update
- Ashley Quarterman joins BCAS as new executive director designate
- BCAS apprenticeship standard coming soon
- Beware non-BCAS members
- A steadying hand in uncertain times
- Compressed air & energy efficiency
- Determining new supplier partnerships
- The need to put safety first
- A look back as a new era begins
- Driving progress in a changing landscape
- MAT - Modular Air Trolley
- Belt drive compressors
- Monitors compressors
- Plugging the skills gap
- Compressor range
- Modular dryer design
- Accurate diagnosis
- Plant complies with latest medical standards
- Hertz Kompressoren UK launches HSC D direct drive air compressor range
- Filter elements tested to ensure air quality