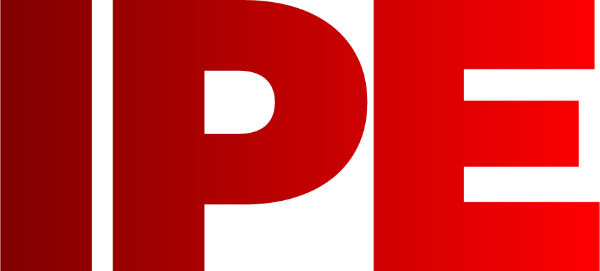
![]() |
Edward Lowton
Editor |
![]() ![]() |
Home> | Production Engineering | >Welding | >Joining the benefits of steel and aluminium |
ARTICLE
Joining the benefits of steel and aluminium
04 March 2013
Steel and aluminium were long thought impossible to join together permanently by thermal means. Here Gerd Trommer explains how Fronius partnered with steelmaker Voestalpine to develop a sheet made of both steel and aluminium, joined by Froniuss thermal joining arc process, CMT (Cold Metal Transfer)
Steel and aluminium were long thought impossible to join
together permanently by thermal means. Here Gerd
Trommer explains how Fronius partnered with steelmaker
Voestalpine to develop a sheet made of both steel and
aluminium, joined by Fronius's thermal joining arc process,
CMT (Cold Metal Transfer)
When comparing steel and aluminium as structural materials, weight, strength, rigidity and workability should be taken into account as well as resource availability and costs. Particularly in lightweight construction, it is often desirable to select an optimum combination of both materials: solid steel for heavy-duty constructional zones, combined with lightweight aluminium for less highly stressed areas.
Until recently arc-joining was not feasible for such joins, despite its many technical and economic merits.
Lightweight constructions deliver benefits in automotive manufacturing. Bodywork accounts for around 40% of a vehicle's weight. If the transport sector's CO2 emissions are to be reduced, weight savings in auto body construction are a place to start. Reducing weight by 100kg can result in 700g/100km fewer CO2 emissions.
Materials-joining technology plays a key role in lightweight construction, particularly when joining steel to aluminium. Fronius partnered with Austrian steelmaker Voestalpine to address this challenge, developing a high-formability hybrid sheet made of both steel and aluminium, joined by Fronius' patented thermal joining arc process CMT (Cold Metal Transfer).
The difficulty in joining steel and aluminium together permanently by thermal means stems from their widely different melting points and, in particular, the formation of intermetallic phases (IMP).The greater the amount of heat inputted into the seam, the thicker the IMP and the poorer the mechanical and engineering properties of the joint. Further challenges result from the widely differing thermal expansion coefficients and the abrupt change in the electrochemical potential. In the light of these physical factors, metallurgists and welding experts have defined the following prerequisites for joining steel to aluminium: The process should generate the lowest possible thermal input.
The surface of the steel sheet must be coated with a zinc layer.
The thickness of the IMP must be minimised.
Joining process Three main factors that influence the formation of a flawless join are the two work pieces to be joined, the joining process and the filler metal.
The aluminium sheets are made from materials of the AW5xxx or 6xxx series. The special gas-shielded arc process CMT fulfils the crucial requirements of the joiningprocess: low thermal input and good controllability. When steel is joined to aluminium, the filler metal and the aluminium wet the galvanised steel sheet and the filler metal fuses with the aluminium. On the steel side, a brazed join is obtained, which the aluminium is then welded against.
For the hybrid sheets, it has been found best to use welding systems which braze-weld 'in sync' with the CMT process on both sides.
The third main factor is the filler metal.
Fronius has a patent for the special aluminium alloy used here in braze-welding.
Steel-aluminium hybrid sheet To explore the product's suitability for actual practice, both partner companies and external institutions performed extensive testing on braze-welded steel-aluminium hybrid sheets using the materials AW5182-H111 and DX54D, and filler metal Z200 made of AlSi3Mn1.
The following tests were carried out: Tensile strength, corrosion test, deformability behaviour and crash-test.
A key result of the tensile test was that final rupture of the sample occurs in the aluminium sheet, with the braze-welded joint surviving the tests intact. The steelaluminium hybrid sheet also survived the salt spray test, with neither crevice/stress corrosion nor intercrystalline corrosion occurring after 300h exposure. The only slight traces of corrosion were on the surface.
The deformability behaviour of the sheets plays a critical role in autobody construction.
The steel-aluminium hybrid sheets were proven suitable for reproducible sheet metalworking.
When they are designed from the outset as safety-critical components, hybrid sheets can systematically absorb accident impact energy. On the hybrid impact absorber, the energy absorption takes place almost entirely in the aluminium part of the component.
Both the braze-welded seam and the steel part of the component are undamaged. In contrast to this, a steel-only component absorbing the same amount of energy sustains more serious damage.
Fronius and Voestalpine have developed a volume-production-ready fabrication process for steel-aluminium hybrid sheets. Extensive testing has proven their practical suitability and additional construction and application benefits in certain cases.
When comparing steel and aluminium as structural materials, weight, strength, rigidity and workability should be taken into account as well as resource availability and costs. Particularly in lightweight construction, it is often desirable to select an optimum combination of both materials: solid steel for heavy-duty constructional zones, combined with lightweight aluminium for less highly stressed areas.
Until recently arc-joining was not feasible for such joins, despite its many technical and economic merits.
Lightweight constructions deliver benefits in automotive manufacturing. Bodywork accounts for around 40% of a vehicle's weight. If the transport sector's CO2 emissions are to be reduced, weight savings in auto body construction are a place to start. Reducing weight by 100kg can result in 700g/100km fewer CO2 emissions.
Materials-joining technology plays a key role in lightweight construction, particularly when joining steel to aluminium. Fronius partnered with Austrian steelmaker Voestalpine to address this challenge, developing a high-formability hybrid sheet made of both steel and aluminium, joined by Fronius' patented thermal joining arc process CMT (Cold Metal Transfer).
The difficulty in joining steel and aluminium together permanently by thermal means stems from their widely different melting points and, in particular, the formation of intermetallic phases (IMP).The greater the amount of heat inputted into the seam, the thicker the IMP and the poorer the mechanical and engineering properties of the joint. Further challenges result from the widely differing thermal expansion coefficients and the abrupt change in the electrochemical potential. In the light of these physical factors, metallurgists and welding experts have defined the following prerequisites for joining steel to aluminium: The process should generate the lowest possible thermal input.
The surface of the steel sheet must be coated with a zinc layer.
The thickness of the IMP must be minimised.
Joining process Three main factors that influence the formation of a flawless join are the two work pieces to be joined, the joining process and the filler metal.
The aluminium sheets are made from materials of the AW5xxx or 6xxx series. The special gas-shielded arc process CMT fulfils the crucial requirements of the joiningprocess: low thermal input and good controllability. When steel is joined to aluminium, the filler metal and the aluminium wet the galvanised steel sheet and the filler metal fuses with the aluminium. On the steel side, a brazed join is obtained, which the aluminium is then welded against.
For the hybrid sheets, it has been found best to use welding systems which braze-weld 'in sync' with the CMT process on both sides.
The third main factor is the filler metal.
Fronius has a patent for the special aluminium alloy used here in braze-welding.
Steel-aluminium hybrid sheet To explore the product's suitability for actual practice, both partner companies and external institutions performed extensive testing on braze-welded steel-aluminium hybrid sheets using the materials AW5182-H111 and DX54D, and filler metal Z200 made of AlSi3Mn1.
The following tests were carried out: Tensile strength, corrosion test, deformability behaviour and crash-test.
A key result of the tensile test was that final rupture of the sample occurs in the aluminium sheet, with the braze-welded joint surviving the tests intact. The steelaluminium hybrid sheet also survived the salt spray test, with neither crevice/stress corrosion nor intercrystalline corrosion occurring after 300h exposure. The only slight traces of corrosion were on the surface.
The deformability behaviour of the sheets plays a critical role in autobody construction.
The steel-aluminium hybrid sheets were proven suitable for reproducible sheet metalworking.
When they are designed from the outset as safety-critical components, hybrid sheets can systematically absorb accident impact energy. On the hybrid impact absorber, the energy absorption takes place almost entirely in the aluminium part of the component.
Both the braze-welded seam and the steel part of the component are undamaged. In contrast to this, a steel-only component absorbing the same amount of energy sustains more serious damage.
Fronius and Voestalpine have developed a volume-production-ready fabrication process for steel-aluminium hybrid sheets. Extensive testing has proven their practical suitability and additional construction and application benefits in certain cases.
MORE FROM THIS COMPANY
- Innovation in welding
- Added functionality
- A weld cladding solution for finned walls
- Complete charging systems
- Welding all-rounder
- Fronius UK to host Back to the Future of Welding event
- Battery charging technology on show at LogiMAT 2018
- Date set for 'Open House'
- New devices for TIG welding
- CMT upgrade for TPS/i Robotics power source
OTHER ARTICLES IN THIS SECTION