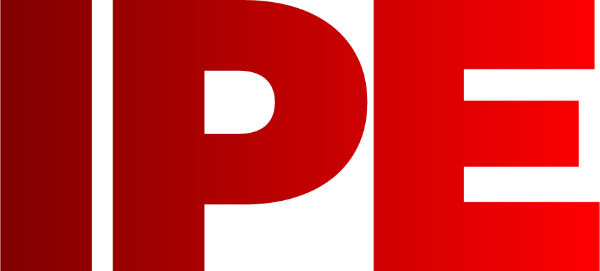
![]() |
Edward Lowton
Editor |
![]() ![]() |
Home> | Plant, Process & Control | >Boilers and burners | >Invest for success |
Home> | Energy Management | >Boilers and burners | >Invest for success |
Invest for success
03 November 2014
The idea that keeping old heat raising equipment up and running will save you money is often a false economy, costing you dearly in fuel, maintenance and operational expenditure. Investing in modern heat raising systems may well pay off relatively quickly, explains Chris Horsley, MD of Babcock Wanson
One of the key developments in the heat raising field that has led to reduced bills is the development of high efficiency thermal fluid heating systems, some of which will include integral economisers to ensure very low fuel consumption even when operating at high fluid temperatures.
There are a number of reasons this type of system has proved popular in industry, but top of the list comes energy savings. Thermal fluid heating systems can use 20 to 50% less energy to transfer the same amount of heat when compared to traditional steam heating systems.
One of the key factors in achieving very high levels of system energy efficiency is the ability of a thermal fluid system to work at high temperatures (up to 350°C in standard form) in a simple closed loop. When compared to a steam system this means no change of state of the fluid so no condensate and therefore no flash steam losses, no blow down losses or make up water required, no effluent discharge and completely corrosion-free without the need for expensive chemical treatment.
Case studies
Wire and Strip manufacturer Webster & Horsfall converted from steam generators to thermal fluid heating in 2011 in its Birmingham premises where it manufactures high-strength drawn wire. A Babcock Wanson TPC600B thermal fluid heating system was fitted to heating tanks for metal treatment, replacing the existing inefficient steam boiler. The new system precisely matches fuel input to plant energy requirements for high efficiency.
As a direct result, Webster & Horsfall has seen a 35% drop in annual kW usage from 2006 to 2011. Robert Horsfall, finance director, is understandably pleased with the savings made: "The new heater is one third more efficient than our previous steam based system, which allows us to operate more efficiently, reduces our energy bills and has a considerable impact on reducing our carbon footprint.”
TRB Lightweight Structures is a further example of investing in equipment in order to save money. TRB is a leading OEM for the rail, aerospace, defence and marine industries, designing and manufacturing tailor-made lightweight solutions and bespoke fabricated assemblies.
The company moved away from steam heated platen presses to a gas-fired Babcock Wanson TPC600B thermal fluid heating and cooling system, whilst at the same time installing new platens. The move has proved good news for TRB as Tim Britt, marketing manager, explains: "We estimate that we have received a 70% cost saving since we have had the new system installed. It’s a cleaner system as it does not corrode and requires less maintenance. We’re obviously not burning heating oil now so our emissions have also been greatly reduced.”
That’s not to say that everyone should run out and buy a thermal fluid heating system today. Steam generators remain an excellent option for some applications and processes - most notably where both direct and indirect heating are required simultaneously. But it might be worth considering moving to the new breed of high efficiency coil type steam generators. They consume less energy, have reduced emissions, offer improved safety and simplicity of control and are considerably quieter, cleaner and cooler in operation.
These are just a couple of examples of savings that can be made by investing in modern heat raising systems. If you are a large energy user, I believe it’s almost a no brainer. But even smaller organisations can benefit from the energy efficiency that these systems can bring. The longer you wait to make the investment, the more it’s likely to cost you.
- SteamPack Fire Tube Steam Boiler
- Rental service
- Regenerative Oxidisers
- Process Air Heaters
- Bulk liquid terminal takes on thermal fluid system
- Low emission burner
- Babcock Wanson acquires Steam Plant Engineering
- Steam raising system on skid or in container
- How to increase firetube boiler efficiency
- Babcock Wanson UK introduces DCT regenerative oxidisers and solvent recovery systems