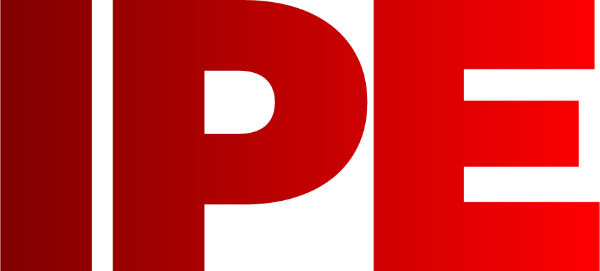
![]() |
Edward Lowton
Editor |
![]() ![]() |
Home> | Plant, Process & Control | >Automation | >How would you address our productivity gap? Let us know |
How would you address our productivity gap? Let us know
18 February 2022
JAMES SNODGRASS

LAST YEAR I visited the Manufacturing Technology Centre near Coventry to chat with chief automation office, Mike Wilson. I was surprised to learn that, despite what seems like decades of decay in UK manufacturing, we’re still the ninth largest manufacturer in the world. Shockingly, though, when it comes to automation, specifically robot density in factories, we rank a lowly 24th. Wilson said: “In order to increase levels of automation, and increase productivity, we need to address the culture in UK manufacturing.”
Now I’ve seen all the documentaries about the decline of manufacturing in the 1970s, with the shots of historian Dominic Sandbrook sighing, nodding his head, and blaming everything on “Red Robbo” the British Leyland trade union activist. “So do you mean the trade unions?” I asked, pretty much expecting the answer to be “yes“.
"Oh no,” said Wilson, “In fact the relevant trade unions understand the benefits and are supportive of the need for greater adoption of automation.” So if it isn’t unions, what is the culture in UK manufacturing that is holding our country back?
The worst idlers in the world
Back in 2012 the then-rising stars of the Conservative Party, Kwasi Kwarteng, Priti Patel, Dominic Raab and Liz Truss, co-wrote a book Britannia Unchained with a withering assessment of British workers: “once they enter the work-place, the British are among the worst idlers in the world”, “we work the lowest hours, we retire early and productivity is poor” and “too many people in Britain, prefer a lie-in to hard work.”
Of course these industry experts were all humanities graduates, and three-quarters Oxbridge. It’s not even true: there are several more productive countries with shorter working hours.
That same year I was on a factory tour in Germany. During a demonstration of two robots, one downed its tools and sloped back to its base position. “Must be British,” I said. The assembled journalists, from across Europe – and further afield – laughed in recognition of a universal truth: Brits are workshy. I took the cheap laugh but felt traitorous.
It’s a national stereotype that Brits are indolent. We’re not. Just like not all Germans are efficient (I’ve flown Lufthansa). Why did we earn this label? It all boils down to the c-word: Cribbins. In his 1962 Top 10 hits, The Hole in the Ground and Right Said Fred, Bernard Cribbins observed British working culture from both sides. In the first, an officious passer-by in a bowler hat thinks he knows better than the road worker. In the second, he sings of a culture of intertia at work: three removal men struggle with heavy loads and so then they have a cup of tea …
Cribbins isn’t really the C-word
The greatest inhibition to productivity in the UK is class division. Not the obvious bowler hat/cloth cap division of Cribbins’ day, more a gap between the mercantile and the industrial, the consultant and the engineer. The mindset of “profit today, don’t worry about tomorrow”. It’s the snobbery that in the 1990s turned polytechnics into universities, to give vocational courses the class cachet of academia – but with the unintended consequence of many polys shedding vocational teaching in favour of academia – thus trebling the pool of graduates whose only skill was bullshitting about French philosophy, and for whom few career routes were available apart from consultancy, politics or worse (e.g. journalism).
Looking back at BL, the “killed by unions” story doesn’t tell the whole story. All businesses had strikes in the 70s. Ford did. Vauxhall did. Yet both these (US-owned) firms managed to erode BL’s market share (in 1970 BL’s Austin/Morris 1100 was the UK’s top selling car, by 1979 it was Ford’s Cortina). What was different about the culture of these US firms? This is not a rhetorical question. I want to know your opinion. Visit IP&E on our LinkedIn page (see left) and we can discuss Britain’s work culture. How would you address our productivity gap?
- Delivering seamless e-Commerce print-on-demand solutions
- Innovate UK funding helps Prior Scientific
- Engineering and manufacturing firms lack awareness of the increase in the Annual Investment Allowance, survey shows
- Technidrive expands Drum Drive range
- Manufacturers take action to tackle growth-harming skills shortage
- Keeping track of critical alarms during a pandemic
- Wood product manufacturer fined after worker dragged into rotating shaft
- Manufacturing business confidence rises for first time since 2018
- Introducing GC1230: The new benchmark in indexable steel milling
- Lights, camera, action …
- Latest software
- Compact robot controller
- Standard machine elements from Elesa
- test baner
- Baking automation
- Higher payload
- Power supplies controlled via web
- New Eiger freezer door installed as business heats up at leading meat packaging company
- Linear and rotary combination
- High temperature chain fluid