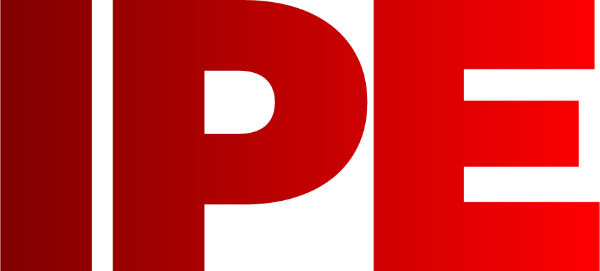
![]() |
Edward Lowton
Editor |
![]() ![]() |
Home> | Efficient Maintenance | >Reliability-centred maintenance | >Severn Trent raises the bar on reliability with condition monitoring |
Severn Trent raises the bar on reliability with condition monitoring
04 January 2024
With an asset base of 538 Rotating Biological Contactors across 326 sites, machine failures could potentially have a significant impact on Severn Trent’s business. This led the company to turn to SPM to help introduce condition-based maintenance technology, creating substantial savings.
THE DEMAND for reliable delivery and regulatory compliance is higher in the water industry than in any other critical infrastructure service. The industry is up against increasingly stricter environmental laws and regulations, and balancing these against tight budgets is a tall order. Utility company Severn Trent turns to condition monitoring to boost reliability and secure delivery.
Equipment reliability is everything
All wastewater treatment plants - industrial, domestic, and agricultural - require regular maintenance to ensure that every piece of machinery operates as intended. Equipment running smoothly and effectively cuts energy consumption and enables higher process efficiency. Failing equipment or processes can lead to costly repairs, secondary damage, poor effluent quality, or pollution, resulting in hefty fines.
Among the various equipment in utility company Severn Trent’s sites, Rotating Biological Contactors (RBCs) are critically important in wastewater treatment in remote areas. The RBC process allows the wastewater to come in contact with a biological film to remove pollutants before the discharge of treated wastewater into the environment. RBCs are an efficient solution for small communities. Rather than incurring costs for pressure and lines to pump sewage to larger works, it can be treated on-site and returned safely to the hydrologic system.
Equipment failure in the RBCs can be detrimental to the environment and costly to repair as it involves tankering and getting cranes out to these remote locations. With an asset base of 538 RBCs in 326 sites, machine failures have a significant impact on the business. Having had costly issues with some of its RBCs, Severn Trent started to look for ways to improve equipment reliability and overall plant efficiency.
Condition monitoring trial
The RBCs are some of Severn Trent’s slowest-rotating assets, with a rotational speed of about 1 RPM. Severn Trent selected thirteen RBCs and embarked on a six-month trial, starting with an MOT service to establish the current equipment condition.
Measuring the mechanical condition of low-RPM machinery with reliable results is notoriously tricky, and different technologies were trialled to determine the costs and benefits of each one. In one particular site, one bearing fault and one gearbox fault were found. The only technology able to pick these up was the SPM HD shock pulse technology; neither ultrasound nor vibration measurement caught these faults. The HD condition monitoring technologies from SPM Instrument provide early warning of mechanical faults and lubrication issues in machines with rotational speeds from below 1 RPM and upwards. Having many low-speed applications, that capacity made the choice of monitoring technology an obvious one for Severn Trent.
Besides the precise and reliable measuring results, a deciding factor in the choice of monitoring technology was the possibility of setting alarm limits in the analysis and diagnostics software.
“We wanted to make it as easy as possible for our personnel in the field to understand and work with the system without needing extensive training,” said Laurence Thomas, asset care senior advisor at Severn Trent. “Until they are fully trained, the software allows our field technicians to react to evaluated machine condition in red, amber, and green. This intuitive user interface enabled us to jump-start our condition monitoring on these critical assets. When called for, technicians can alert maintenance managers to study the measuring results in more detail”.
On the RBC systems, Severn Trent takes monthly measurements on the drive- and non-drive- end bearings using handheld instrumentation. Due to its excellent measurement performance on machinery with very low rotational speeds, measurement is done with the SPM HD shock pulse technology.
Condition-based maintenance - a winning strategy
In a condition-based maintenance strategy, equipment condition and performance are monitored, continuously or periodically, to determine the most cost-efficient time to carry out maintenance.
Despite its many advantages, it is not unusual for condition monitoring to be a relatively unfamiliar concept in some maintenance departments, while, in others, it might be met with a degree of skepticism. Thus, one of the most significant challenges in implementing a condition-based maintenance strategy is getting everyone in the organisation on board. The strategy needs to be anchored in company culture and organisational responsibilities. Having staff on various levels buy into the concept, accept change, and commit to the process is a critical success factor. Demonstrating results to staff involved in maintenance is equally important to overcome resistance and promote commitment.
However, a successful condition-based maintenance strategy does not happen overnight. It requires attention, conviction, and diligence from the top down.
Slow and steady wins the race
Keen to get things right from the start, Severn Trent takes a systematic approach to implementing its condition-based maintenance program on a larger scale. The change from reactive to proactive and predictive maintenance is an incremental process. Installation of condition monitoring equipment, software for measuring results analysis, and personnel training are all carried out gradually across Severn Trent business areas.
To ensure the necessary skills, a long-term employee training plan has been established for the involved staff. The field technicians undergo training in steps, starting with a bespoke, one-day basic training, where they learn how to handle the handheld measuring units, make individual measurements, carry out complete measuring rounds, and upload the data to the analysis and diagnostics software. To support the field technicians, the maintenance managers have a higher level of training. They, in turn, can reach out to the Severn Trent Asset Care team for further assistance if needed. This "competence hierarchy," backed up by the condition monitoring supplier's deep knowledge, ensures that Severn Trent can take advantage of the benefits of condition monitoring to improve operational reliability and availability significantly. The ultimate goal is for all the relevant maintenance staff to go through three levels of training.
Once the condition-based maintenance is fully implemented across all business areas, maintaining the right competence in the maintenance department is a project in itself, as is continually communicating its successes, impact, and overall benefits.
On the importance of demonstrating the value of condition monitoring to obtain staff engagement, Thomas noted: “For us, it is about communication, really, and sharing some of the successes that we have had. We also try to motivate the staff by showing them that some routine maintenance tasks will need to be carried out considerably less often with condition monitoring in place. A good example is the intrusive inspections, which, in the case of the RBCs, is a big job”.
To further establish the benefits of the condition-based maintenance strategy throughout the organisation, findings and experiences are shared at monthly meetings in a reliability group with participants from various functions within Severn Trent. They also take part in collaboration meetings with other UK water companies.
Early warning is vital
On the RBCs, around-the-clock operation is required. Hence, there is no optimal time to do maintenance, which makes prewarning times an essential factor. The bacteria need to be constantly fed, and if they are not, it takes about a week to get them built up and back in the process. A one-day maintenance stop is okay from a microorganism point of view, but in the case of a 12-18 week stoppage - the average lead time for the delivery of spare parts in the wake of the pandemic - an extra week must be added for the build-up of the biofilms on the discs.
Substantial savings
Given the long lead time on spare parts, repairing catastrophic failures on the RBCs is about £20,000 in repair bills on average. On the smaller sites, tankering alone costs about £400 per day. With condition monitoring in place, costs have dropped to approximately £5,000, including labour, parts, and crane hire.
When factoring in RBC capital costs, being able to react to problems early enough to get the RBCs back in service within a day is favourable. Condition monitoring saves Severn Trent substantial amounts in capital costs.
A concrete example of savings made possible through condition monitoring is significantly lower lubricant costs. The monitoring system’s capacity to determine lubrication condition and alarm levels fine-tuned to provide sufficiently early warning of lubrication issues makes it possible to optimise the choice of lubricant as well as lubrication schedules.
The measurements have shown that using the wrong kind of grease for the conditions and environment in which RBCs operate reduces bearing life by about 80%. By switching to water-proof grease repelling the ambient moisture, grease costs have dropped from around £18 per tube to about £2.40-2.70. Optimised lubrication routines also enable a decrease in time spent on intrusive inspections.
Since starting the implementation of condition monitoring, Severn Trent has identified a few cases of gearbox damage. Generally, though, the mechanical condition of RBC bearings and gearboxes overall is good at the sites where condition monitoring has been rolled out so far - in part due to the change of lubrication media.
Plans going forward
One of Severn Trent’s main objectives in the long term is to bring as much corrective maintenance work as possible back in-house rather than having subcontractors or service companies do the work.
“If the stub shaft fails on the drive-end side of an RBC, it might cost over £80,000 if we need to get a new gearbox,” explained Thomas.
“Getting the stub shafts out without damaging them can be problematic, and in the process, there might be consequential damage to the gearbox as well, so we are trying to reduce that kind of catastrophic failure. Because we now detect any problems early enough, we need to replace the bearing only.
“Our outfitters can do that a lot easier and will be trained to do it in-house. Bringing more corrective work back in-house will enable us to stay more on top of costs because markups are significant, and we can do the work a lot cheaper ourselves,” he continued.
“It is not just about the cost, though - it is about work fulfillment as well. If our technicians are completing the corrective work, they feel a lot more engaged in their work. As such, condition monitoring is an enabler for them.”
Further trials planned
In addition to monitoring the mechanical condition of RBCs, Severn Trent has also conducted successful trials on wastewater screw pumps, using handheld units and online systems with HD condition monitoring technology. Early warning of machine faults on this process-critical equipment can reduce the need for temporary overpumping systems to keep the service uninterrupted during maintenance and repairs, which costs about £10,000 per week.
The condition monitoring system also protects against the risk of overflow, which is a substantial cost saving in pollution fines.
For Severn Trent, the high costs of failure and workarounds are key motivators for including screw pumps in the condition monitoring programme.
On the clean water side, a trial is planned on motors and pumps using handheld measuring equipment. At three of its Bioresources sites, Severn Trent has recently installed online systems on high-speed gas-to-grid compressors. Furthermore, wireless vibration sensors are being trialled on gas-to-grid engines.
For more information:
Tel: +46 152 225 00
- Troubleshooting software
- SPM Instrument launches revolutionary measuring technique for condition monitoring
- SPM Academy's condition monitoring courses
- Vibration-only measuring unit
- Online system for Ex environments
- Low speed solution
- Online condition monitoring system
- Predicting faults all over the world
- For continuous monitoring
- Paper mill opts for new measurement tool
- Distribution
- Reliability strategy: New thinking required
- RCM : The quest for easier implementation
- Strong cast for Maintec theatres
- Top tips to keep your belts in business
- Boosting the scope of shrink fits with engineering adhesives
- Advanced pump analysis proves invaluable
- Hydraulic equipment maintenance & improvement
- Keeping your diesel engine healthy
- Optimising machine reliability