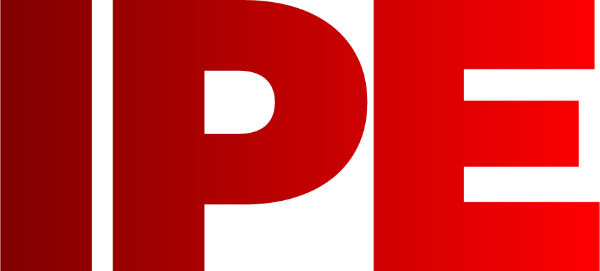
![]() |
Edward Lowton
Editor |
![]() ![]() |
Home> | Plant, Process & Control | >Robotics & Automation | >From skills shortage to tech triumph |
From skills shortage to tech triumph
02 September 2024
Given the skills shortage, manufacturers should consider alternative strategies to fill the gap, says Mikko Urho

MANUFACTURERS CAN no longer rely on a steady flow of readymade skilled employees. The UK is facing its most significant shortfall in skilled workers since 1989, with factors such as economic instability, the cost of living, Brexit, Covid-19 and changing age demographics all coming together to leave 77% expressing concern about their ability to make new hires. Without these skills, firms will struggle to commission, design and optimise their production systems, including their robotic deployments.
Supporting short-staffed teams
Where talent pipelines are drying up, manufacturers need to look at alternative strategies to fill the ever-widening skills chasm. Robots can fulfil a range of functions that humans would traditionally handle. Welding, cutting, painting and other processes can be performed with robotic deployments.
But for robots to be put to task, they need to be manually programmed, which requires a specific human skill set of its own and a significant amount of time. According to research undertaken by Visual Components of manufacturing decision-makers in the UK, the manual programming process can take between a week and a month for over a third of manufacturers (35%). It’s essential that staff are provided with the tools to get robots up-and-running and build their skills on the factory floor.
Offering upskilling opportunities
Offline robot programming (OLP) provides a digital model of a robot and its work cell, and via a simulated interface, movements and workflows can be fully replicated and tested before a real-world deployment takes place. Typical programming problems, such as collision avoidance and joint-limit violations, can be solved with automated capabilities.
OLP provides a number of additional benefits. Programming can take place concurrently as the robot is deployed, hugely reducing the time to becoming fully operational. Software is able to recognise features of a workpiece or component, such as holes or pockets, and work this into programming procedures. Crucially, however, OLP offers the chance for employees to upskill in programming robots to complete a task, all in a flexible way.
Leading OLP solutions are intuitive, logical and easy to use, encouraging novice users, even non-engineers, to quickly become proficient in robot deployments. Different robot brands can all be managed and controlled to effectively complete tasks. The technology is also suited to remote working practices, allowing employees to complete the process from anywhere. With the knowledge and expertise stored in the system, manufacturers avoid the issue of it potentially leaving the business when skilled staff leave or retire.
Turning a challenge into an opportunity
OLP not only enhances the efficiency and accuracy of robotic tasks, but also offers crucial upskilling opportunities for the workforce. With intuitive software available, novices can build their skills and bring robots to the production line, all without the costs and time that would otherwise be spent doing so. Manufacturers may have little control over the availability of specialist-skilled workers, but technology-driven transformation to support the current employee base is very much within their power.
Mikko Urho is CEO at Visual Components
For more information:
Tel: +358 9 252 40800
- Emergency preparedness pack launched for businesses
- €50m funding for Irish SMEs
- UK manufacturing hamstrung by skills and Brexit in digital adoption
- Sensor specialist sets up new safety division
- Embrace the crisatunity, business-as-usual is complacency
- Robots help engineering firm embrace smart factory innovation
- How to outsource manufacturing effectively
- Questar demonstrates predictive maintenance solution
- Manufacturing companies repurpose facilities to combat COVID-19
- Digital adoption critical for an enterprise-led recovery
- Latest robots: Slim and easy to install
- APP that controls robots
- Collaborative robots: Risks and rewards
- Precision bearings aid smart grasping
- Collaborative robots: Safety matters
- 3D simulation program for robot control
- Bearings chosen for robotic exoskeletons
- Cobot collaboration delivers entry-level vision-guidance
- Robots boost profitability for machining company
- Entry-level vision-guided cobot system