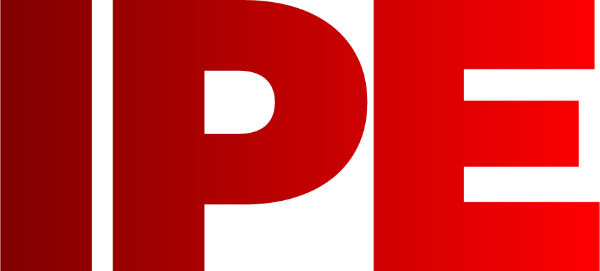
![]() |
Edward Lowton
Editor |
![]() ![]() |
Home> | Efficient Maintenance | >Industry 4.0 | >Finding the perfect balance with autonomous maintenance |
Finding the perfect balance with autonomous maintenance
15 August 2022
Forward-thinking companies are levering smart solutions to enhance knowledge-sharing, improve collaboration and make better-informed decisions about their assets, says Chris van den Belt

MINIMISING EQUIPMENT failures and downtime is key to greater productivity and profitability in industrial manufacturing. However, at the same time, maintenance costs must be kept in check and all relevant safety requirements adhered to.
When a fault occurs in the production line and the plant comes to a standstill, quick action is needed. But before anything can be done, several questions must be answered. Who will perform the maintenance to get everything back up and running?
The easiest answer would be the operator on site since they are standing next to the machine, but do they have the skills, tools and experience required to repair it? If support is necessary, will it be provided by the in-house maintenance team or an external service provider? How much will the repairs cost, and how quickly can they be carried out? And how is the safety of the people, equipment, and products, and compliance with regulation guaranteed during this time?
The situation can be stressful for everyone involved, from the plant operator to the production staff and the maintenance team. Still, managing the complexity is part of everyday life in most modern production environments. Over 60 percent of asset managers surveyed in the latest Enterprise Asset Management (EAM) Trend Report 2021 admitted to suffering unplanned downtime in their facility in the past year.
Enhancing information-sharing
Poor communication and problems sharing essential information are repeatedly cited as the biggest factors putting uptime at risk. It is, therefore, hardly surprising that companies see improving internal processes around these areas as key to futureproofing operations.
All too often, maintenance, repairs, and asset condition data is stored in Excel spreadsheets, on paper-based lists, or, worse, in the heads of those involved. This can significantly disrupt information-sharing between departments and make achieving a holistic view of all assets and the related performance and cost factors impossible. To make well-founded decisions regarding maintenance and repairs, managers need to have the maintenance data readily available to them.
Managing asset data with EAM
An easy way to address these challenges is by digitising the data and the related processes, for example, with an Enterprise Asset Management (EAM) system. Modern EAM solutions, such as Ultimo, have been developed to collect, share, and analyse asset data and host it in one place to make it easily accessible to all stakeholders to enable well-informed decision-making. They provide companies with a comprehensive view of their asset health and the related cost and performance.
Cloud-based EAM software makes the asset data available to every authorised user on their laptop, tablet, or smartphone. It is also easy to view historical maintenance data or remotely guide operators working on the machinery. Managing jobs, checklists, and the related documentation within the EAM system helps ensure that all tasks are performed consistently across different teams and sites, simplifying how knowledge and best practice is shared and retained within the company.
Sharing responsibility
However, while having a robust EAM system in place lays the groundwork for improving knowledge-sharing and productivity, there is still untapped potential for increasing maintenance efficiency.
Optimising uptime is a goal shared by maintenance staff, process managers and plant operators, but the perspective can differ significantly between departments.
While production managers demand the highest possible plant availability and see insufficient maintenance of assets as the likely cause of failure, maintenance managers often associate downtime with operator failures, lack of opportunities to carry out preventive maintenance, and limited maintenance budgets. Process managers and HSE departments, on the other hand, are likely to blame downtime on the challenges posed by the lack of communication and transparency between departments. These disagreements can result in frustration and dissatisfaction between teams, possibly putting downtime and safety at risk.
One way to address this is through shared responsibility. Looking after equipment and conducting repairs is no longer the sole duty of the maintenance team: the plant operators can be given joint responsibility for the condition of the machinery and the continuous improvement of productivity.
After all, they are the closest to the machines, know how they run, and can often spot an impending failure far in advance, perhaps simply by the noise the machine makes. If a fault is identified, the operator can react immediately and take any necessary action instead of waiting for the maintenance team to come to fix it. As well as quicker, direct action is often more cost-effective than calling a technician, especially with recurring minor repairs.
Maximising internal resources
For this approach to be successful, however, organisations need to have a clear and straightforward system in place for recording and sharing vital asset information.
Ultimo addresses it through its Autonomous Maintenance module, which makes it possible to transfer the responsibility for completing and reporting specific maintenance tasks such as cleaning, inspection and lubrication to those who operate the machine. This gives them more control over its condition and demonstrates that the knowledge and experience they’ve gained through working with the equipment is acknowledged and appreciated.
Yet, despite the potential benefits, sharing responsibility requires continuous training. Here, the maintenance team can help, as removing the need to tend to minor maintenance tasks increases their capacity for other, more value-adding activities. They can devote more time to strategic, forward-looking maintenance management and operator training and development.
Benefits of one system
Documenting and storing the operator’s observations in the same EAM system used by the maintenance team eliminates the risk of any knowledge gaps. Together with modules that cover other key functionalities supporting autonomous operation, such as Downtime Registration and Shift Handover, it provides maintenance and operations teams with an easy-to-use platform for collaboration.
The modules allow operators to register downtime incidents and keep a log of any anomalies, and the information is available to their colleagues at shift changeover. The process helps ensure that all essential knowledge relating to the assets remains within the company, both teams have constant real-time access to it, and that no vital detail gets lost through lack of communication.
Using one platform to manage all the processes can also help enhance safety. Maintenance work is often a major source of risk when it comes to health, safety, environment and quality (HSEQ) management. Some EAM systems take this into consideration, with Ultimo, for example, integrating QHSE processes to simplify compliance.
The software is designed to ensure that maintenance tasks can take place only after the required safety measures have been completed. The step-by-step function makes maintenance safe and easy, simplifying passing responsibility for some jobs to the operator. At the same time, all actions are documented in Ultimo, ensuring a clear trail of the work that has been done and eliminating the risk of duplicating tasks.
The perfect balance
With a range of advantages at grasp, it’s no wonder asset managers are recognising the role of intelligent software solutions in improving knowledge sharing. An advanced EAM solution is an invaluable tool for helping provide the insight needed to implement well-planned and cost-efficient maintenance measures and enabling quick action in case of an acute system failure.
Moreover, the right EAM software helps enhance cooperation between plant operators and the maintenance, benefiting the entire organisation. By helping redistribute the responsibilities through autonomous maintenance, companies can make the most of their available resources, optimise collaboration between operators and the maintenance staff, and, ultimately, boost productivity and profitability
Chris van den Belt is product team leader at Ultimo
For more information:
Tel: 0161 615 3685
- SolutionsPT partners with IFS Ultimo to optimise asset management portfolio
- Ultimo announces UK partnership with DNASTREAM
- Optimising data-driven maintenance
- Ultimo and Mainnovation join forces
- Ultimo and Axians announce technology partnership
- New features added to EAM software
- Enterprise Asset Management Trend Report
- IFS Ultimo and ALLIANT RIGSERV sign partnership to optimise maintenance and improve safety for asset-intensive customers
- Prevent depletion of your assets; three tips
- IFS Ultimo supports Orkla's digital transformation
- Technology and Open Standard data enabling smart maintenance
- Broadband sensors: Pinpointing leaks in compressed air systems
- Mechanised welding, cutting and Industry 4.0
- Tomorrow’s tech is here today
- Investment in infrastructure, innovation and people
- Getting to 4.0 – one hard-won gain at a time
- Digital transformation in the chemical industry: White paper
- Digital industry around the world
- Guidance via AR
- How machine learning is transforming predictive maintenance