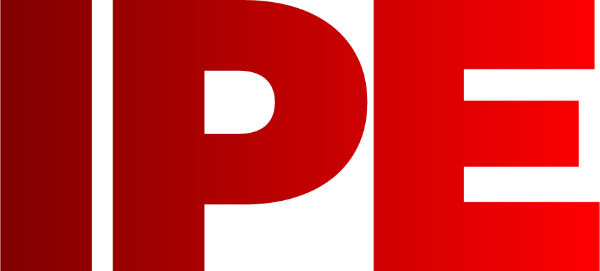
![]() |
Edward Lowton
Editor |
![]() ![]() |
Home> | Production Engineering | >Deburring equipment | >Self-contained blast room upgrades production |
ARTICLE
Self-contained blast room upgrades production
25 January 2013
Production facilities at specialist pipeline valve manufacturer, Oliver Twinsafe, have been upgraded with the installation of a self-contained Enviraclean blast room with abrasive recovery system and high-performance
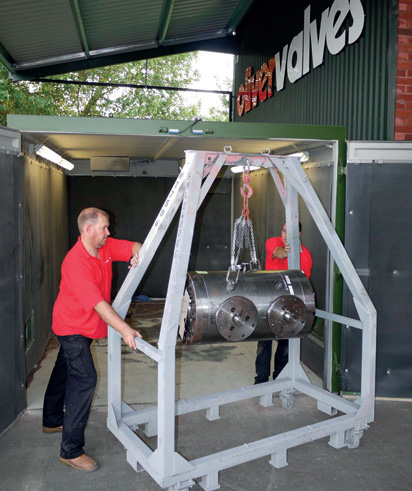
Production facilities at
specialist pipeline valve
manufacturer, Oliver
Twinsafe, have been
upgraded with the installation
of a self-contained
Enviraclean blast room with
abrasive recovery system and
high-performance sound
insulation from Hodge
Clemco.
The chamber measures 4m long x 3m wide x 2.5m high and has double access doors at one end to accommodate large components. The walls are lined with rubber curtains to reduce abrasion, and modular double-skinned panels have an acoustic lining to reduce the noise that can be heard outside the chamber during blasting. Air inlet ducts and exhaust outlets are designed to provide effective ventilation in order to ensure good visibility for operators. Media is projected by a 2452 SGV blasting machine via a 3/8 inch (10mm) ID tungsten-carbide-lined nozzle, which is designed to maintain maximum blasting velocity, uniform abrasive distribution and high work-rate over a long operating life.
Abrasive is recovered for re-use by means of a pneumatic suction filter unit linked to a sweep-in hopper in the floor of the blast room.
The chamber measures 4m long x 3m wide x 2.5m high and has double access doors at one end to accommodate large components. The walls are lined with rubber curtains to reduce abrasion, and modular double-skinned panels have an acoustic lining to reduce the noise that can be heard outside the chamber during blasting. Air inlet ducts and exhaust outlets are designed to provide effective ventilation in order to ensure good visibility for operators. Media is projected by a 2452 SGV blasting machine via a 3/8 inch (10mm) ID tungsten-carbide-lined nozzle, which is designed to maintain maximum blasting velocity, uniform abrasive distribution and high work-rate over a long operating life.
Abrasive is recovered for re-use by means of a pneumatic suction filter unit linked to a sweep-in hopper in the floor of the blast room.
MORE FROM THIS COMPANY
- Self-contained blast room
- Finishing system boosts throughput
- Quieter approach to surface preparation
- Blast cabinets help upgrade aircraft maintenance facilities
- Self-contained production rooms
- Blast room investment
- Choice of service packages
- Giant blast-room installed
- Customised blast cabinet
- Finish quality upgrade
OTHER ARTICLES IN THIS SECTION