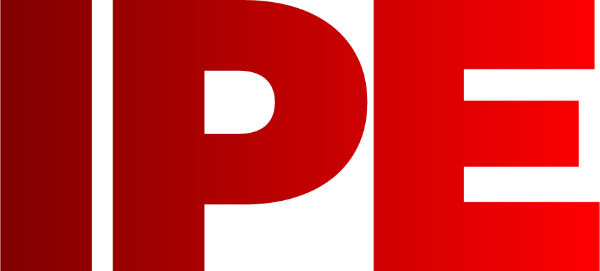
![]() |
Edward Lowton
Editor |
![]() ![]() |
Home> | Handbooks | >AirUser | >Controlling water contamination |
Home> | Energy Management | >Compressors & ancillary equipment | >Controlling water contamination |
Home> | Plant, Process & Control | >Compressors and ancillary equipment | >Controlling water contamination |
Controlling water contamination
23 July 2013
Three basic contaminants need to be considered with regard to compressed air systems – water, solid particles and oil. Here, Ben Rickards, product technical manager at Norgren, focuses on water.
Compressed air can be an expensive energy source if equipment is incorrectly sized, managed and maintained. Air produced by a compressor is often hot, wet and dirty, containing contaminants which must be reduced to an acceptable level before it enters the main system and, if needed, further treated at point of use to ensure optimal air quality while minimising the risk of corrosion and other damage.
Water frequently originates at the compressor outlet in vapour form, but as the air cools, will be present in liquid form too. Most liquid water will exist when the temperature is lowest and the pressure is highest, meaning removal at this point will be most efficient. The compressor system should be fitted with an aftercooler of sufficient capacity to cool the outgoing air to within 8°C of the temperature of the water entering the aftercooler.
The outgoing air should be piped to a receiver in the coolest available location - not within the compressor house – to enable further cooling, condensation and removal. Generally, receiver capacity should be around thirty times the compressor’s rated free air.
Distribution mains should have a pitch in the direction of air flow so gravity and air flow will carry water to drain legs. All air take-off points from the distribution mains should draw air from the top of the main to minimise water ingress.
Water can be removed via drip leg drains, automatic drain valves and filters. As air can cool when passing through distribution mains and branch lines, smaller individual filters should be installed as near to air usage points as possible. Filters should always be located upstream of any pressure-reducing valves.
To remove water vapour, air dryers must be employed. Efficiency is increased by ensuring driers are not contaminated by liquid water or oil and are supplied with air as cool as possible.
In refrigerant driers, air passes across a heat exchanger containing a coolant. As air temperature drops, water vapour condenses into liquid and is removed. Generally air exiting the dryer passes into a higher ambient temperature meaning no further condensation occurs.
In regenerative adsorbent desiccant driers, desiccant material absorbs water vapour from air passing over it, reducing the air’s dew point. The desiccant material can only adsorb a given amount of water before it saturates, but can be dried out and reused. Some driers incorporate two 'towers' of desiccant material and a heater, with one tower being dried and regenerated while the other continues to remove water vapour. Deliquescent absorbent driers are similar except that the drying material is ultimately dissolved into the adsorbed water.
Membrane driers pass air through semi-permeable membranes with the water vapour passing through the membrane by plasmolysis (reverse osmosis). As water vapour is removed from the air, the dew point is suppressed - the level of suppression is related to the contact time with the membranes and the pressure. Low flow and high pressure deliver the lowest dew points.
Dryers are expensive in terms of acquisition, filtration equipment, pressure drop (running costs) and maintenance. To minimise costs, system designers should consider whether drying is required or if efficient aftercoolers, receivers and filters will suffice. Very low dew points should not be specified unless the process warrants them, while the volume of air being dried should be only that needed for a particular process. This will generally result in small discrete driers placed only at processes which require air to that quality, creating a cost saving against supplying the whole plant to that standard.