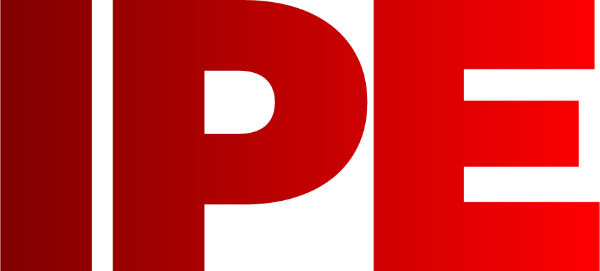
![]() |
Edward Lowton
Editor |
![]() ![]() |
Home> | Handbooks | >AirUser | >Keeping the pressure off |
Home> | Energy Management | >Compressors & ancillary equipment | >Keeping the pressure off |
Home> | Plant, Process & Control | >Compressors and ancillary equipment | >Keeping the pressure off |
Keeping the pressure off
03 July 2014
Compressed air must be used at the ideal pressure to optimise return on investment. Higher pressure can cause excessive wear without significant output increase, while, too low a pressure may not do the job effectively or quickly enough. Ben Rickards, product technical manager at Norgren, explains
If the compressed air is stored at this higher pressure and only used at exactly the level required for the application, the storage vessel or receiver needs only to be topped up to the full capacity.
To achieve this, the compressor usually operates between two pressure levels, with a pressure switch set to give compressor cut-off at the required storage pressure and a lower level usually about 10 to 20% lower – meaning it is not running continually.
Excessive compressor pressure generates more heat and thus more water, increasing processing costs and still supplying air at too high a pressure for no output increase.
Cylinders rely on inlet pressure to generate the required force. If the generated air from the compressor is supplied directly into the mains, pressure will vary both from the compressor loading and also as other plant processes demand air, reducing pressure in the distribution ring main. This will result in varying force from the cylinder, affecting process quality.
The solution is a pressure-reducing valve designed to maintain constant outlet pressure irrespective of inlet pressure (the regulation characteristic) and outlet flow (flow characteristic).
The penalty for poor regulation is varying outlet pressure, while poor flow characteristics can create pressure drop which affects energy costs. Every regulator suffers from some pressure drop so system design must address this.
Pressure regulators require a supply pressure at least 1 bar higher than the required outlet pressure. They will work with a lower differential but performance can be impaired.
Regulators broadly comprise four types: general purpose, pilot-operated, precision and special purpose. A regulator which controls the pressure to a distribution main is usually general purpose, or pilot-operated for large volume/flow applications. Once established whether a standard or precision regulator is needed, the suitability of the regulator flow capacity for pipe size needs must be decided.
If there is no inlet pressure variation, the regulation characteristic of the regulator is unimportant but the flow characteristic will be. If the inlet pressure is exposed to variations, the chosen regulator’s regulation characteristics must also be considered. Ideally regulators should be operated inside the middle third of their range. Low-rate springs can also help reduce pressure drop, so springs can be selected to best fit system requirements.
If a precision regulator is required, the level of sensitivity, flow and regulation characteristics, and, if necessary, relief capacity and temperature sensitivity must be established.
Most precision regulators employ a constant bleed of air, so have a constant air demand, even under ‘no flow’ conditions. Correct selection could see a general purpose regulator with ordinary performance characteristics fulfilling what may be considered a precision regulator’s function without system degradation at lower installed cost and with reduced air demand.
Filter/regulators clean the air and control pressure in one compact unit, usually more cost-effectively than separate units, while ensuring the regulator is optimally protected.
Where a compressor directly supplies cylinders, product quality will be optimised by controlling the inlet pressure with a general purpose regulator, while energy costs can be substantially reduced by using double-acting cylinders where a reduced pressure can be achieved on the non-working return stroke.
Selecting and installing the correct type and size of pressure regulator will ensure optimal performance and energy efficiency.