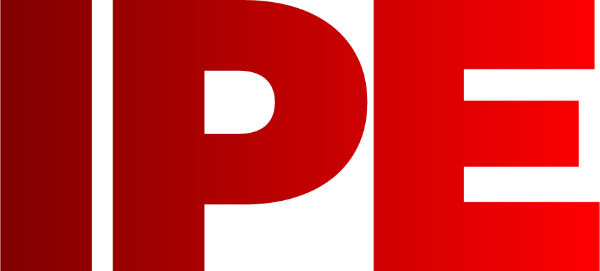
![]() |
Edward Lowton
Editor |
![]() ![]() |
Home> | Plant, Process & Control | >Valves and actuators | >Valve actuation: Reliability is key |
Valve actuation: Reliability is key
02 December 2016
With their various ports and fluid paths, solenoid valves offer flexibility. When chosen and used appropriately they can provide safe switching, reliability, durability and resistance to extreme conditions, extensive lifespan and compact design. Richard Harvey of IMI Precision Engineering explains more
Solenoid valves must be suitable for the application and able to resist corrosion, dust, water and other environmental aggression, for many years, and must have suitable hazardous area and safety certification. However, historically they have often been seen as the weak link in the final element assembly as they are often chosen based on cost and not design.
Dangerous failures
A dangerous failure prevents the solenoid valve from performing its safety function when required, on demand, and often occurs because friction and stiction have increased over time. The load holding the valve open increases to the point where the spring force is no longer sufficient to close the valve. A dangerous failure occurs when spring force < friction + retentivity. The ratio of the spring force to the friction and retentivity (force friction ratio (FFR) can be improved by:
- Minimising the number of dynamic seals - these add friction to the design
- Increasing spring force
Safe failures
In safety related systems it’s important to periodically test all the final elements (to prove the safety function is working to the required performance), and test the solenoid valve in addition to the actuator and process valve. The biggest concern when solenoid valves are tested is safe failure, of which there are two types: spurious trip (which occurs during normal operation); and failure to operate on demand, which causes a spurious trip during partial stroke testing (PST).
One example of a spurious trip could be where the solenoid coil burns out, there is a loss of magnetic flux and thus the process valve closes. The safe failure rate will be improved if burn-out can be prevented, in which case the following may apply:
- Reduce the coil running temperature
- Ensure efficient thermal dissipation
- Use an integrated core, armature and coil construction
The second type of safe failure is when valves fail to open on demand, termed a pull-in failure. Over a period of time, cable damage or termination corrosion can cause an increase in resistance leading to reduced voltage at the solenoid valve coil. Here, the voltage may fall below the required pull-in voltage. During a PST, the solenoid coil is de-energised and then re-energised at the end of the test. However, while the coil voltage was sufficient to hold the valve in the open position, it is insufficient to pull-in (re open) the valve from its closed position. As a result, the process valve completely closes, causing an unintended trip. This can be avoided by checking the coil voltage prior to initiating a partial stroke test.
One way to improve safe failure rates is to improve magnetic flux as this allows higher margin of flux over spring force. Fortunately, there are several ways of promoting optimal magnetic flux. Most solenoid valves use a wet armature arrangement where the internal magnetic components are exposed to the instrument media. Therefore a corrosion-resistant material must be used. Unfortunately, such hard magnetic materials reduce the maximum magnetic flux and increase retentivity. In contrast, a dry armature, where the magnetic components are isolated from the instrument media, allows for soft magnetic materials to be used which exhibit increased maximum magnetic flux and reduced retentivity.
When looking to improve magnetic flux, the core design, and in particular the magnetic path integrity, should also be considered. A core tube design leaks magnetic flux as there are air gaps between the coil and the tube, whereas an integrated design maximises flux strength.