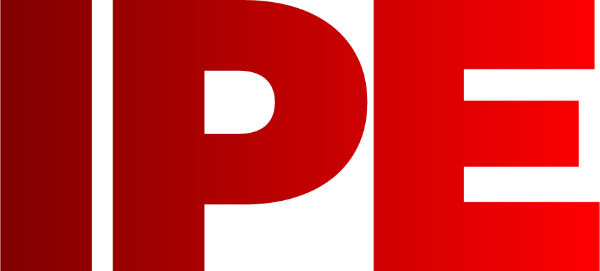
![]() |
Edward Lowton
Editor |
![]() ![]() |
Home> | Handbooks | >AirUser | >Bacteria and condensate |
Home> | Energy Management | >Compressors & ancillary equipment | >Bacteria and condensate |
Home> | Plant, Process & Control | >Compressors and ancillary equipment | >Bacteria and condensate |
Bacteria and condensate
23 July 2013
While Beko Technologies' sales and service staff may hear expressions of pride and satisfaction about a new compressor or the energy saving performance of a dryer or intelligent control system, there's not the same excitement over a new condensate management system – until there is a problem. Here, Chris Norris UK service manager explains more about the less glamorous side of the compressed air business
Beko Technologies has built its business on the back of its expertise in compressed air condensate management – that is draining and separation. There are many variables – type of compressor oil, environmental contaminants and temperature – to name just a few, so there are possibilities for failure that need to be considered.
The sad fact is that condensate management is about box ticking. The factory engineer has many issues with which to contend, things that could go wrong, improvements to consider and cost savings to achieve. However, condensate management is something he has to do – no choice – and with no major benefit to the way his department runs (of course the benefit is to us all in terms of protecting the environment).
So he has purchased and installed a unit and now he wants to forget it. Sadly not really possible. Water contains bacteria which cannot be removed by conventional filtration. Bacteria multiply rapidly and under normal conditions 1 bacterial organism per millilitre will grow into more than 1,000,000 colony forming units within one working shift! Bacteria will also produce slime and can produce 100 times their own volume.
So it is evident that if unchecked this will become a serious problem. The outcome possibly will be that on some low cost systems the unit will appear to be working but the filter will be inefficient and condensate with too much oil entrained will go to the drain and contaminate our water resource. Significant fines could be levied too. The other possibility is that the unit will no longer be able to flow the volumes of condensate and will overflow. This is not tolerable, but at least the condensate is not reaching the water table and rivers and the engineer has a signal that action has to take place.
Beko Technologies has solutions for these scenarios. When purchasing a condensate management system, the company strongly advises users to think about their situation. Type of oil and local contaminants will be known and if there are any doubts Beko Technologies will analyse a sample of condensate as part of the service, thus enabling a definitive comment on the type of management system required. It is well known, for example, that the printing industry, due to the volatile organic compounds used, will not normally have condensates that will separate, i.e. they will remain in colloidal suspension. These systems will require a splitting system which introduces a material which will 'split' the oil by combining with it and being easily removable in that combination. The Bekosplit product is well proven for difficult condensates over many years.
Beko Technologies has also developed a system which can overcome the issue of blocking and blinding by forcing flow using a pump system. The flow control device uses the company’s level sensor technology to measure the condensate level within the Owamat. Once the preset level is reached the flow control unit pumps condensate through the Owamat filter and to drain. The flow control system overcomes the problem of slime blocking the filter sets. This problem of slime will affect all brands of oil and water separators which have the relevant bacteria present in the condensate.
For customer who suspect they may have problems with their condensate system and the law, Beko Technologies is offering a free site survey to inspect and test condensate systems to ensure customers legal obligations are being met.