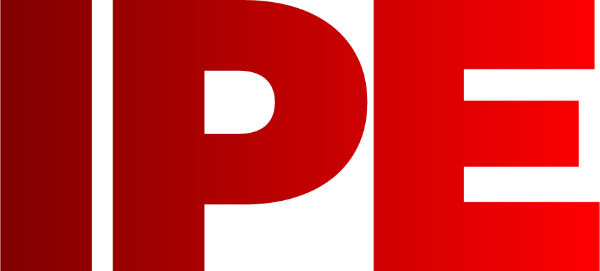
![]() |
Edward Lowton
Editor |
![]() ![]() |
Home> | Handling and Storing | >Lift trucks & ancillaries | >Charity benefits from 400,000th truck |
Charity benefits from 400,000th truck
21 January 2016
To celebrate production of the 400,000th truck at its Craigavon plant in Northern Ireland, Yale Europe Materials Handling has made the largest single charitable donation in its history. Val Kealey visited the site to find out more
As the specially manufactured 400,000th truck rolled off the production line, employees at the Craigavon factory marked the milestone by handing it over to Oxfam, for the international charity to use at its distribution centre in Bicester, Oxfordshire. The Yale Veracitor VX was signed by all staff at the Craigavon factory and was presented to Oxfam GB’s finance director, Alison Hopkinson, by Craigavon plant manager Jim Downey.
Behind the scenes planning for the charitable donation began many months ago, with the technical team from Yale asking Oxfam exactly what sort of truck would suit its needs in terms of capacity, capability and fuel type. By liaising with the logistics manager from Oxfam, UK territory manager for Yale, Andrew Hine, specified that the 400,000th truck should be a GDP/GLP20-30VX model, selected for its manoeuvrability, reach and ease of use.
The Veracitor VX,offers innovative technology to reduce brake and tyre wear, longer service intervals, and built-in fuel efficiency. The Yanmar 2.6L diesel engine consumes as little as 3L/h, while the LPG engine range is said to deliver new levels of performance.
At Oxfam’s Bicester warehouse a variety of load sizes and weights are handled. Items used to be manually weighed on scales prior to dispatch via air freight around the world. Yale’s partner, RAVAS donated i-Forks for the 400,000th truck to save Oxfam time by automatically weighing the load when it is lifted. Yale’s UK dealer, Briggs Equipment, has offered to maintain and service the truck.
Iain Friar, Yale brand manager, said: “Yale is committed to ‘people, products and productivity’ and we firmly believe that it is our people who have put us where we are today. The 400,000th truck is the embodiment of the innovative approach and loyalty we receive from our Yale people."
The current workforce numbers about 570 and, while the average length of service is 17 years, the plant has 62 people with more than 30 years’ service
It takes around four days to produce a truck at the site and current production level at the Charlestown Road plant is an average of 54.5 trucks a day. Plant capacity is 100 units per day, although the optimum day rate is 90 (around 20,970 a year).
Products manufactured at Craigavon include: 1.6 to 5.5t internal combustion counterbalanced lift trucks (4 product series) and 1.3 to 5.5t electric counterbalanced lift trucks (5 product series).
Plant manager, Jim Downey explains that a key challenge has been to make the manufacturing facility as lean as possible. He says: "The challenge has always been to keen the site as competitive as possible by manufacturing quality products at the lowest cost and in the safest manner and, to do that, we are constantly looking at how we can develop our people. The key to our success is our people. We're constantly training and developing our people to make them more effective. We're constantly looking at our processes and how we operate those processes. Could we do things differently, use different techniques, etc."
The site's commitment to its people was highlighted last year when Craigavon again received the Gold Investors in People Award from Employment and Learning Minister Stephen Farry.
The plant continues to look to the future. While the assembly process is manually intensive, the company is looking at different processes for how it welds truck frames and masts. It recently introduced two new ABB robots for miscellaneous welding. Jim Downey explains that one of the benefits of these is that they are better for the environment: "With the two new robots, the weld system is enclosed. Filtration systems on top of the robots allows us to filter the weld fume and pump it back into the environment as fresh air. We have a vision that at some stage when you walk into our manufacturing area there will be no weld fumes. It's quite a clean environment already, but we want to eliminate weld fumes altogether."
The company believes the driving force behind its successes its commitment and implementation of the Yale tagline 'People, Products, Productivity' and this includes integrating the company's assets to achieve operational excellence through technology, processes and people engagement. Iain Friar adds: “We believe it’s truly a team effort that’s responsible for impressive Yale history and longevity in this very demanding industry.”
- Productivity model
- Efficiency boosted by new steering system
- New mast design
- Yale releases MR reach truck
- Redesigned controls for latest pedestrian stacker
- 5 ways warehouse equipment can improve productivity
- New heights in productivity
- More comfort & visibility
- Pedestrian stackers
- Ready for action – whatever the weather