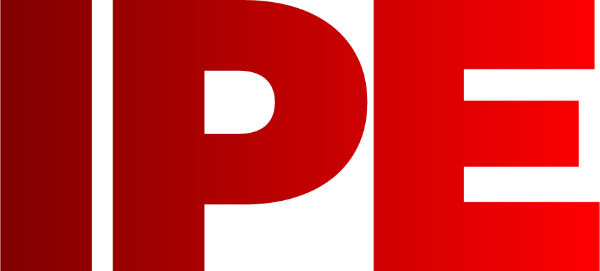
![]() |
Edward Lowton
Editor |
![]() ![]() |
Home> | Handbooks | >IPE Ireland | >Scientific approach to workholding |
Home> | Production Engineering | >Machine centres and tools | >Scientific approach to workholding |
Home> | Handbooks | >Manufacturing Matters Ireland | >Scientific approach to workholding |
Scientific approach to workholding
24 October 2017
With increasingly complex component designs and expanding capacity demands for turned parts, Prior Scientific recently installed a new Mazak QT250 twin spindle turning centre with both C and Y-axis capability. It opted for workholding equipment from Hainbuch.
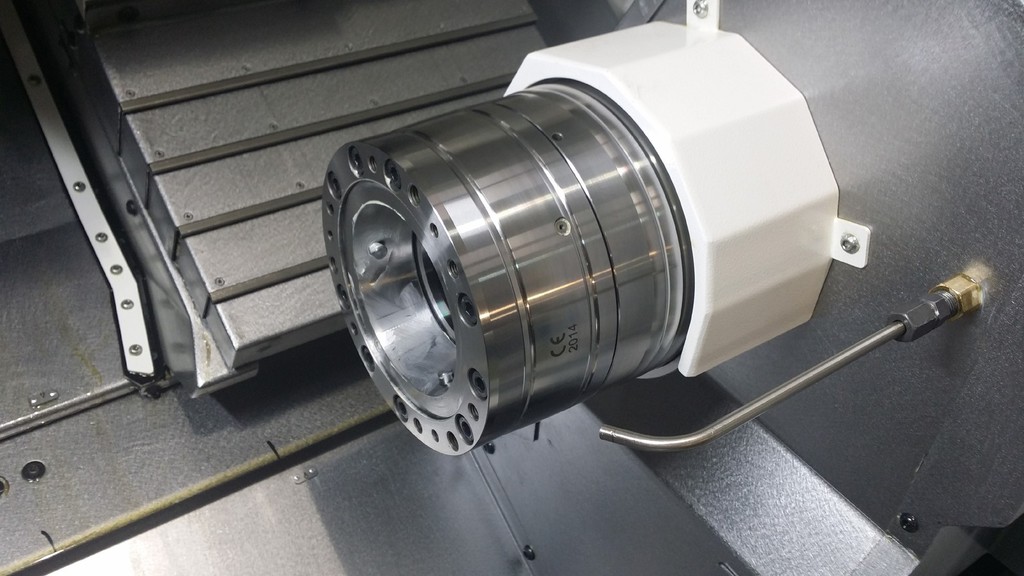
As Prior Scientifics’ machine shop manager, Roberta Harder says: “We manufacture parts from a range of materials, diameters and lengths with quantities than can vary from 5 or 10 up to 200+. With frequent changeovers, we needed a quick change system that would allow us to switch from a vast array of collet diameters up to 65mm as well as offering the ability to clamp larger billets when necessary.”
To achieve this, Hainbuch recommended its Spanntop collet chuck with the addition of its jaw module and mandrel system. By specifying the additional modules, Prior Scientific can rapidly change from a collet chuck configuration to a 3-jaw chuck with the ability to clamp billets up to 215mm in a matter of just 30 seconds. With the Mazak QT250 being a bar-fed turning centre, the Hainbuch Spanntop system enables Prior to change from bar-fed production work that demands precision collet clamping to front loaded large billet machining with a 3-jaw chuck.
The uncompromising precision levels at Prior Scientific noted the company specifying a Hainbuch Spanntop pull-back collet chuck on the main spindle and a dead-length Spanntop collet chuck on the sub-spindle. This configuration guarantees consistent precision levels on both main and sub-spindle. To address any concerns over clamping forces and part marking, Hainbuch supplied a complete series of smooth and serrated collets. The serrated collets are applied to a vast array of component types that vary from heavy duty robust turning through to the clamping of brass that frequently causes slipping and consistency issues with oily residue and its outer skin.
Commenting upon the application of the Hainbuch Spanntop collet chucks, Roberta Harder says: “We bought the Mazak to eliminate secondary operations which would subsequently improve quality. The other key factor was to increase productivity. The collet chucks play a vital role in both facets of our aims. Firstly, the wide range of collet and chuck options gives us great flexibility. Added to this, the fast changeover of collets and even the change from collets to the 3-jaw chuck configuration reduces non-machining times and supports our aims of optimising machine utilisation. From a quality perspective, precision clamping is assured through the zero-point configuration and the pull-back principle of the Hainbuch Spanntop Series.”