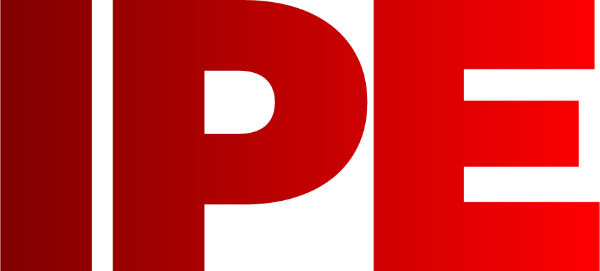
![]() |
Edward Lowton
Editor |
![]() ![]() |
Home> | Energy Management | >Compressors & ancillary equipment | >Strong voice in uncertain times |
Home> | Plant, Process & Control | >Compressors and ancillary equipment | >Strong voice in uncertain times |
Strong voice in uncertain times
22 January 2018
The Brexit process and safe piping, are topics tackled by BCAS (British compressed Air Society) in this issue of IP&E
We are now half way through the Brexit process and are still waiting to find out what the business landscape might look like after March 2019. Companies do not like uncertainty and the management of events through next year is vital if we are to mitigate the consequences and make the most of any opportunities.
As the UK’s trade association representing the compressed air and vacuum industry, BCAS is currently working with a number of other industry groups to ensure that business gets the best deal it can beyond Brexit.
For example, BCAS’s work in international standards and legislation will be critical as organisations work through the implications of the Great Repeal bill. One of the most important areas to pay attention to will be divergence – we already work in a complex environment where businesses struggle to understand their commitment to legislation and with more companies operating as European and Global entities, further complexity will only add to the cost of production and maintenance.
For businesses, the challenge of making sure that the UK voice is heard is important as it will influence how equipment is designed in the future. It is fair to say that the UK has punched above its weight in Europe in this area compared to how much it exports.
In this global era of manufacturing, BCAS continues to be a strong voice in legislation by working in partnership with Pneurop, Orgalime and CAGI.
Safe piping
In our ongoing series looking at the safe and efficient application of compressed air, BCAS talks us through the design and installation of piping and the procedures to follow during commissioning.
Supplier selection
The first area to consider is the selection of a suitable and competent supplier. Under Regulation 6, The Pressure Systems Safety Regulations 2000 Approved Code of Practice, the owner/user of the system must ensure that those carrying out the installation have the required training, skills and experience.
While the Regulations do not specify piping types or specific installation procedures, it is important that the user selects a supplier that can demonstrate competence through experience and evidenced training in pipe installation and jointing, including an understanding of safety issues and the demonstration of safe working practices.
To demonstrate compliance with the law, users (and their contractors) should follow ‘good industry practice’ during the installation process – such as trade bodies’ codes of practice; for example; the ‘BCAS installation Guide’ and the ‘BCAS Pressure & Leak Testing Best Practice Guide (BPG 103).’ These publications cover the selection of equipment, correct installation and commissioning prior to use.
Installation Guidelines
The next area to focus on is the installation itself to ensure compliance and safety.
The air mains can be sited at any level from under-floor ducting to overhead. For ease of servicing and draining and for access when connecting to service points, the overhead main is often used.
Safety in commissioning
Once the installation has been carried out to the appropriate recommendations, the air pipe systems should then be tested before use to establish the leak rate for energy efficiency and reliability, and to verify the integrity of the pipe/fittings joints to ensure personnel safety.
This means that two distinct tests must be completed; the leakage test and the pressure (integrity) test.
Before carrying out these tests, a risk assessment procedure and method statement should be drawn up to establish which areas would be dangerous to personnel should there be a major leak or system failure – and the appropriate precautions taken.
Where there is an extension to an existing system, then only the new part of the system should be tested. The existing system should not be pressure tested and should be isolated before pressure testing commences. Subjecting an old system to a pressure test of up to 1.5 times operating pressure could over-stress it and lead to its premature failure.
For further information, please visit bcas.org.uk
- Working together to navigate Brexit:
- BCAS supports new UK-based supply chain development platform
- UKCA update: "Clarity cannot come soon enough"
- Providing stability in uncertain times
- Getting to grips with legal matters
- Simple steps to compressed air energy savings
- Taking an energy-first approach to compressed air system design
- Understanding PSSR 2000
- BCAS appoints new president
- Training: An ongoing requirement