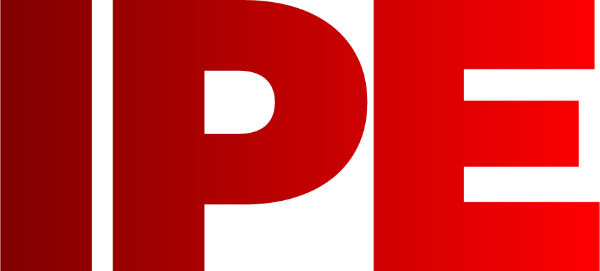
![]() |
Edward Lowton
Editor |
![]() ![]() |
Home> | Production Engineering | >Machine centres and tools | >Collet changeover times slashed |
Collet changeover times slashed
29 July 2015
When torque control equipment manufacturer, Norbar, invested in a new Mori Seiki turning centre and a Matsuura VPlus800 machining centre to boost productivity and capacity, the Banbury-based company wanted to explore how to reduce non-cutting times through innovative work-holding solutions. Hainbuch provided a solution.
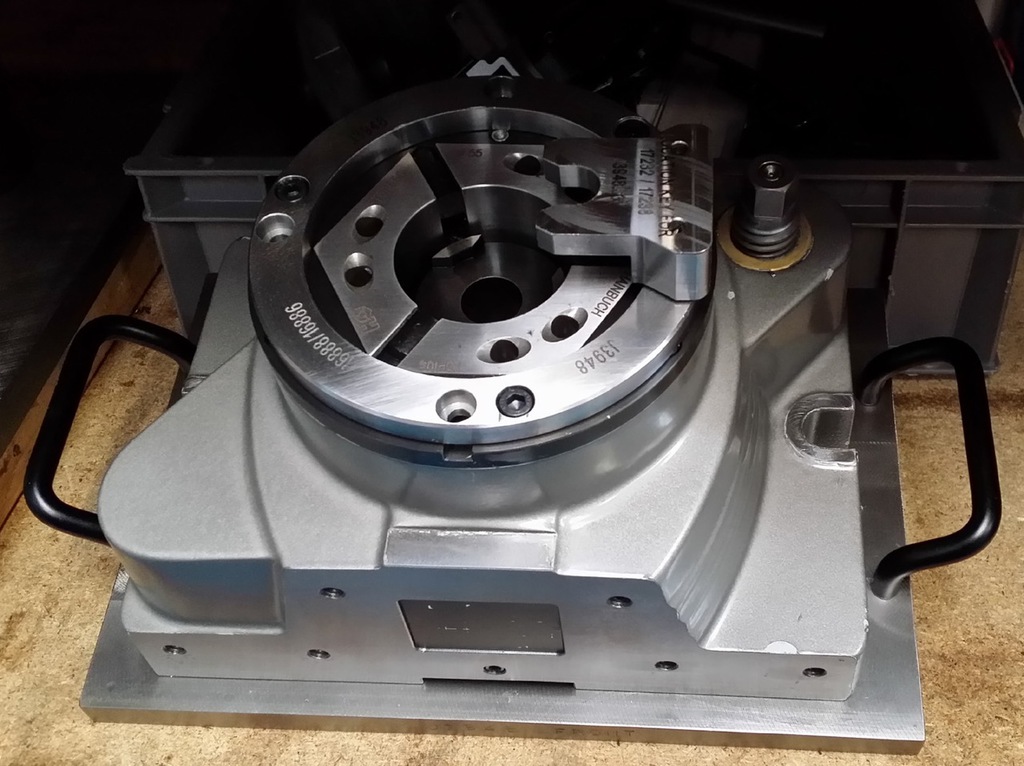
Norbar engineers researched various work holding solutions and opted to invest in the TOPlus system for its 65mm diameter bar capacity Mori Seiki turning centre.
Producing planet gears and sun gears for its carrier gear sets, Norbar's new 65mm TOPlus collet chuck from Hainbuch is now permitting collet changeover times in 30 seconds compared to the previous 3 to 4 minutes. As a company that operates a three-shift system with upwards of three changeovers for each shift, the savings and set-up time reductions are such that Norbar is considering a program to install the TOPlus on all its turning centres.
With component batch sizes in the region of 20 to 50 parts, re-setting times are a major factor and the problem with Norbar's existing work-holding is that the faceplate has to be removed via its 12 bolts. This is what incurs the 4 minute change-over time and is something that has been eliminated with the TOPlus.
The TOPlus is said to permit 25% higher clamping forces. One such development is the new pyramid arrangement of glide surfaces that increase clamping forces and this is complemented by the clamping head rests that offer full-surface contact in the TOPlus chuck body. This allows the TOPlus to provide a concentric precision of 0.015mm for chuck sizes to 100m bar capacity.
Norbar recently installed a Matsuura VPlus800 machining centre and the company opted for the Manok stationary clamping system from Hainbuch. The key feature behind this purchase is the flexibility of using the collets across both the TOPlus and Manok systems for flexibility and repeatability. Norbar initially put the Manok system to the test by machining EN24T steel carrier bodies with heavy 10mm depths of cut. The Manok system eliminated vibration and movement whilst providing a robust platform that can extend the longevity of the company's cutting tools. Upon witnessing this success, Norbar also applied the Manok to work in conjunction with a zero point system that enables it to remove and replace the system on the work envelope with speed and precision.
Commenting upon the installation of the two new systems, Norbar production engineer, Darren Smithson says: "Both the TOPlus and the Manok are great systems, they have helped us improve throughput in the factory. They are easy to us and amazingly quick to set up."