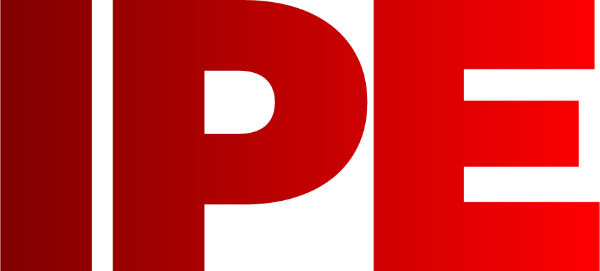
![]() |
Edward Lowton
Editor |
![]() ![]() |
Home> | Handling and Storing | >Batteries and chargers | >Charging technology boost battery availability |
Home> | Handbooks | >Manufacturing Matters Ireland | >Charging technology boost battery availability |
Charging technology boost battery availability
18 June 2018
CEP service provider, TNT uses 14 chargers from Fronius for the forklift fleet at its logistics hub in Vienna
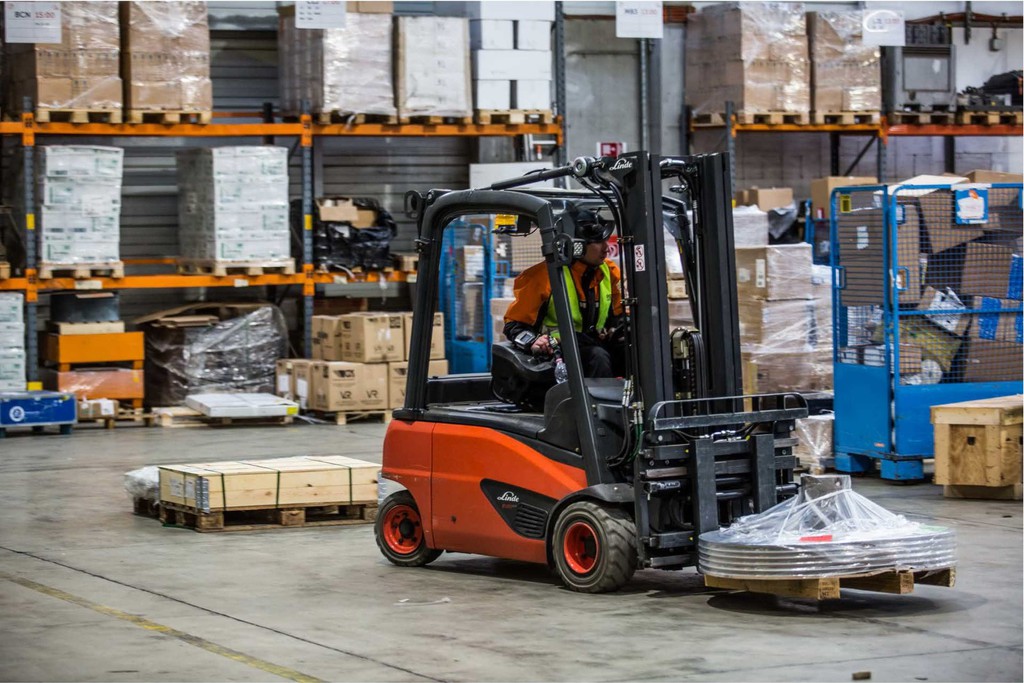
The fleet of forklift trucks is in virtually constant use. These battery-operated forklift trucks are charged at irregular intervals and generally only for a short period. In the past this used to have a considerable detrimental effect on the capacity and service life of their traction batteries, all the more so since the company was still using outdated 50 Hz chargers. Innovative technology from charging technology specialists Fronius allowed this situation to be rectified. TNT can now depend on the intelligent Ri charging process and a variety of individual characteristics to charge any battery according to its requirements at any given time. This not only prevents damage to the costly batteries, but also enables significant savings to be made on energy consumption.
The logistics hub of CEP service provider TNT in Vienna is a real hive of activity: one truck after another pulls up at one of the building‘s many loading bays and is unloaded and reloaded at top speed. Airfreight containers from Vienna-Schwechat Airport, located just a stone‘s throw from TNT, release consignments sent from the four corners of the world from within their bulbous forms. Forklift trucks carry pallet cages full of packages requiring onward transportation through the halls. There are several conveyor belts that sort separate consignments and convey them in the blink of an eye to the correct destination so that they can reach their respective recipients reliably and on time.
This is TNT‘s main site for handling deliveries to and from eastern Europe and also its logistics centre for the entire postal region of Vienna. 80 percent of these goods are transported by road, which equates to 75 trucks entering and leaving the site every single day. No consignment is ever held here for longer than twelve hours. To save personnel the trouble of having to load consignments individually, they are combined in pallet cages. The company handles 300 such containers in an average working day. However, this number can increase significantly during the Christmas period.
TNT has a workforce of 56,000 in 61 countries, making it one of the largest CEP (courier, express and parcels) service providers in the world. The company‘s head office is in Hoofddorp in the Netherlands. It sends out around a million parcels, documents and freight consignments per day – chiefly to corporate customers such as Apple. Its customers demand high levels of punctuality and reliability, so TNT relies not only on a comprehensive and high-performance logistics network, but also on an efficient flow of goods within its sites. There is a fleet comprising 20 electrically-powered forklift trucks of varying sizes available for this purpose – from small pedestrian-controlled trucks to counterbalanced trucks. “We operate a three-shift system here from Sunday evening through to Saturday afternoon”, explains supervisor Dietmar Landor. “This means that our forklifts can be running for up to 3000 operating hours per year.”
Opportunity charging
This long-term usage places considerable strain on the batteries. Irregular charging times and short opportunity charges are the order of the day. Although the large trucks have back-up batteries, changing the battery is often too time-consuming for employees. “Instead the trucks are often just connected to the charger for a few brief minutes, during a work break for instance”, explains Landor. The situation is essentially the same for pedestrian-controlled trucks: “They are charged as necessary, and when an employee needs a forklift they simply take the first one that comes to hand”. However, the incomplete charge cycles have a significant negative impact on the capacity and service life of the traction batteries.
In the past, for TNT this frequently resulted in battery faults and failures. On average, the company used to have to change three of the batteries per year, and with a purchase price of several thousand euros each, that was a costly business that significantly compromised the cost effectiveness of the fleet. The high current consumption of these forklift trucks presented management with an additional headache. It didn‘t take long to discover the reason for this: “We were using outdated chargers with 50Hz transformer technology” says Landor. “They were responsible for a huge amount of energy loss, and the frequent battery faults could also be attributed to the poor charging equipment.” These bulky chargers took up too much space. TNT therefore decided to bring its battery charging systems right up to date.
In the quest to find an appropriate solution, the company came across the Selectiva range from Fronius, the Austrian specialist in battery charging technology. This range incorporates Active Inverter technology and the Ri charging process, using methods for charging traction batteries that are currently the most advanced. The charging process does not follow a fixed characteristic, but adapts itself according to the age, temperature and condition of the connected battery. This ensures that charging is extremely energy efficient and gentle, resulting in less power being used and an increase in battery service life and performance. “We started by presenting TNT with a calculation that showed how our technology could significantly reduce their operating costs”, recalls Alexander Thier, area sales manager at Fronius Perfect Charging. TNT followed up by consulting other experts, a process that left them totally convinced. In 2013 they invested in their first Fronius chargers.
TNT now uses 14 chargers from Fronius. There are six Selectiva Plus chargers in the 3kW power category for the 24V traction batteries in the small pedestrian-controlled trucks. The larger forklifts are equipped with 48V batteries. There are eight 8kW Selectiva chargers installed in a second charging station. These chargers have a compact design and are take up much less space than their predecessors. This gives the forklift trucks more room in which to manoeuvre. TNT is extremely impressed with the charging performance: even with irregular and short charging times, the forklifts still remain available at all times and breakdowns occur much less frequently. “This is due to the variety of characteristics that enable the batteries to always be charged efficiently in accordance with their requirements at any given time”, explains Thier.
Whilst the fleet is at work, with the halls operating at full capacity and the forklifts in almost constant use, a pulse charge provides the vehicles with the maximum possible fresh energy in a short space of time. During quieter phases such as during the night, the intelligent Ri process extends the charging time for as long as possible. This is kind to the battery and helps it to regenerate. At weekends or on holidays, equalisation and conservation charging is carried out. The chargers also have a refresh characteristic that enables sulphated batteries to be reactivated. “Each battery receives exactly the type of charging that it needs”, summarises Dietmar Landor, and this is plain to see: “Since we have been using Fronius technology we have only had to replace one battery, whereas we used to have to replace several every year.” As a result, the fleet operating costs have been reduced significantly.
The current consumption is reduced considerably, and this has a significant part to play in cost reduction: Fronius charging technology minimises the overcharging that produces the high energy losses seen in other processes. This means that TNT is saving money with every charge: “We have analysed our current consumption ourselves so that we have dependable facts to fall back on”, explains Landor. “The calculation that Fronius did for us was correct, and our energy requirements are now greatly reduced.” This is of great benefit to TNT not only from an economic but also from an environmental perspective. As like all Austrian companies, the company is obliged to meet stringent energy-efficiency regulations. This charging technology makes a significant contribution in this respect.
The chargers are said to be very easy to use: the external automatic Start-Stop system means that our employees only need connect and disconnect the batteries; everything else takes care of itself. Another nice touch is the LED strip on the device, which shows if the connected battery has been fully charged and has now cooled down.“ This helps us achieve a much more uniform utilisation of the forklift trucks and batteries”, explains Alexander Thier, Fronius‘s specialist in this field. This too has a positive effect on battery service life. Another useful feature offered by Selectiva chargers is a USB interface, which enables settings such as characteristics to be copied and loaded onto other devices. The user can also download and analyse statistics relating to previous charge cycles in order to match various parameters even more accurately to the specific requirements.
- Welding all-rounder
- CMT upgrade for TPS/i Robotics power source
- Platform for advancements
- Features for steel
- Added functions
- Battery charging division on board
- Battery charging technology on show at LogiMAT 2018
- Portable MMA off-grid welder
- Fronius UK to host Back to the Future of Welding event
- New management