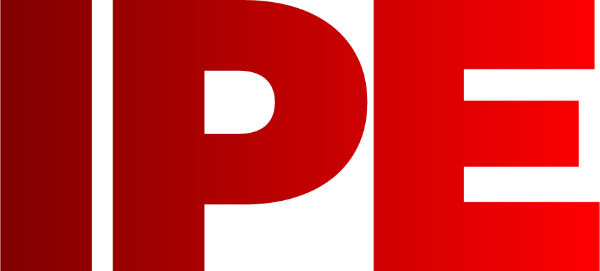
![]() |
Edward Lowton
Editor |
![]() ![]() |
Home> | Efficient Maintenance | >Reliability-centred maintenance | >Reducing total cost of ownership via compressor maintenance |
Reducing total cost of ownership via compressor maintenance
21 August 2023
THE COST of operating and maintaining a compressed air system is an important consideration for industrial manufacturers. Rising energy costs are impacting on new capital investment, with many projects that had extended payback periods previously, now falling under much closer economic scrutiny and viability.

Compressor maintenance is an important factor to include in managing the total cost of ownership, and operators are keen to make savings wherever possible. Here are some top tips to keep compressed air systems running at peak performance.
Prioritising effective compressed air maintenance
Compressors can operate for long running hours and in harsh operating conditions, which can all contribute to higher costs - and greater wear and tear.
Whether as part of a planned, proactive or predictive service plan, maintaining the system correctly will guarantee reliable operation to avoid production downtime, while also ensuring improved energy performance.
Regular maintenance of the compressed air system will help retain low leak rates and reliability of equipment, which combined with a policy that prioritises the purchase of energy-efficient options when replacing compressor equipment and ancillaries, can pay dividends.
Compressor location
Position compressors in a dry, clean and cool location. Not only is more energy required to compress warm air but, higher temperatures can also result in more frequent compressor downtime, leading to a less efficient system.
It is essential for the space around the compressor to be well-ventilated, so operators may want to consider investing in extra ventilation to keep the compressor room as close to ambient temperature as possible.
As much as 95% of the energy consumed by a compressor is converted to heat and, unless captured, will be wasted to the atmosphere. Many manufacturers offer heat recovery and ducting systems, which can often be retrofitted. This allows operators to capture and reuse this excess heat; for example, re-directing the hot oil to an oil-to-water heat exchanger.
System first
Although a compressed air system is a sophisticated piece of engineering, in its basic form it is a ‘system’ and will require regular maintenance to help ensure performance is maximised.
Inlet filters should be inspected and replaced routinely to avoid pressure drops, and any ancillary equipment, such as dryers, filters and air receivers checked regularly.
With the cost of energy high on the agenda, leak detection and pipework maintenance are a vital component of a service plan, as this can be one of the simplest ways to save electricity - and improve performance.
One 2mm hole in the pipework could cost over £1,249 per year in wasted energy, but as air leaks aren’t hazardous to health and safety, other maintenance tasks have tended to take priority.
There a four common leak sources to be aware of, these include air-using equipment left running when not needed; manual condensate drain valves left open; leaking hoses and couplings and leaking pipes and pipe joints.
Identifying the leak
To reduce leaks, operators should conduct an out of hours survey and walk the site listening for any leaks - these should be easy to hear when the site is quiet.
Following the survey, a leak management programme can then be implemented by marking the leaks, recording them on a site plan and grading the priorities, such as fixing the largest leak first.
Finally, as part of ongoing housekeeping measures, staff should be encouraged to report leaks so they can be identified and repaired as soon as possible.
Pressure reduction
When pressure drops in the system it means the generating pressure is set much higher than necessary. This could be a result of system component constrictions (e.g., valves, bends), undersized piping or the original pipework installation.
So, once any leaks have been identified and repaired, operators should speak to their supplier about reducing the generation pressure at the compressor.
Understanding the system pressure is critical when it comes to leakage reduction and reducing energy usage. For example, fixing a leak will increase the pressure of the air generated. This can not only have an impact on the system but also put any projected energy savings at risk.
When it comes to the energy used, on average it is found that for every 1 bar g of additional generation pressure there is a loss of 7% in specific energy. And so, keeping pressure low can help to reduce your operating costs.
The pressure drop should also be less than 10% of the compressor’s discharge pressure, as measured from the compressor outlet to the point of use.
If one section of the plant requires much lower pressure, it is advisable to install a dedicated low-pressure compressor or to regulate the pressure down that line.
Pipework zoning
The design and installation of the pipework can help with saving energy and so when considering leak reduction measures, it is important to consider the pipework currently in place.
There are numerous ways to improve pipework efficiency, starting with the simple measure of removing or isolating any redundant piping and selecting large radius bends instead of elbows to assist air flow.
Not all parts of the network operate to the same hours or pressure and so it’s possible to save energy by zoning the compressed air system and pressurising each as required.
Finally, intelligent installation and design, such as using valves to isolate parts of the distribution network and supporting piping to minimise movement and sagging, which can help reduce leaks and build-up of fluid.
The benefits
The benefits of a full and effective maintenance regime are many and varied. The compressed air system should function much more efficiently, and businesses can help avoid the cost of unplanned outages and downtime.
By implementing a thorough maintenance and service plan, customers can also avoid unnecessary energy loss through poorly performing equipment - freeing up more time to prioritise other energy saving measures.
If you are considering upgrading your existing compressed air system, always speak to an expert. BCAS members can advise on the best equipment and system for your needs. This could include incorporating fixed and variable-speed drives or a combination of both as well as efficient downstream equipment. Where suitable, sophisticated control systems can help proactively manage the supply of air.
For more information, please email [email protected]. And to download a free copy of the latest maintenance guide, please visit: tinyurl.com/25h2cy7w
British Compressed Air Society
Tel: 0207 935 2464
Email: [email protected]
Web: www.bcas.org.uk
- Trade associations: Delivering benefits to members
- The benefits of on-site nitrogen generation
- Air of expectation
- CSCS card update: The current state of play
- Seeking new efficiencies
- Bureaucracy's the bugbear
- Setting a new standard
- Standards and Codes of Practice
- BCAS: GB/UK legislation update
- A look back as a new era begins
- Distribution
- Reliability strategy: New thinking required
- RCM : The quest for easier implementation
- Strong cast for Maintec theatres
- Top tips to keep your belts in business
- Boosting the scope of shrink fits with engineering adhesives
- Advanced pump analysis proves invaluable
- Hydraulic equipment maintenance & improvement
- Keeping your diesel engine healthy
- Optimising machine reliability